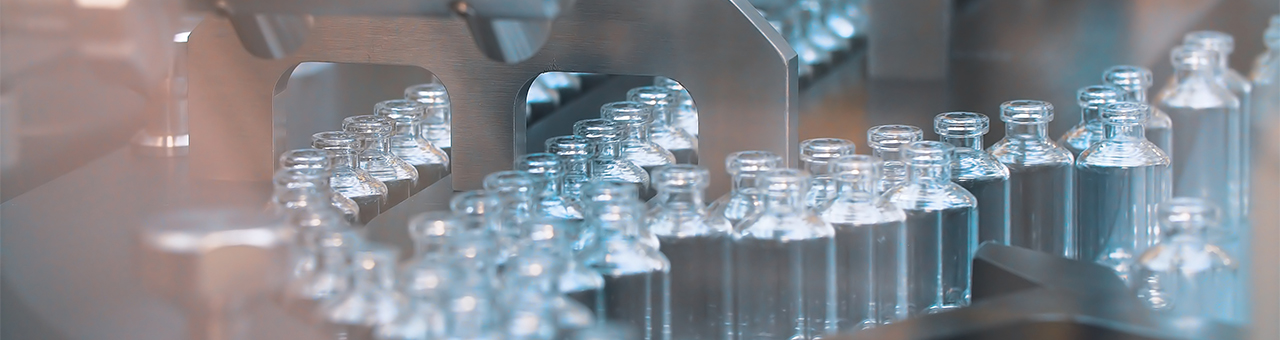
Late Phase to Launch
As clinical development concludes and your process/analytics/quality systems begin to lock down, activities now focus on ensuring you have the infrastructure and capacity to meet commercial requirements. Securing multiple, high-volume batches of vector to meet growing demand and addressing the high (direct and indirect) cost of goods are significant challenges.
Supply:
How to establish a
secure supply chain
Vector On Demand
As you prepare a drug for launch it is critical for your raw material supply chain to be secure. Establishing a secure vector supply chain is one of the most challenging activities for cell and gene therapy companies due to the unpredictable and poorly scalable nature of traditional manufacturing.
iVexSol’s Intelligent Manufacturing avoids these challenges by generating a virtually inexhaustible master cell bank of vector-producing cells. When additional vector is needed, a vial of vector-producing cells is thawed from the MCB, expanded, the vector can then be harvested and ready for release in weeks, not months or years. iVexSol’s ability to produce “vector on demand” de-risks vector supply and avoids the need to stockpile or purchase a large inventory of vector to avoid supply issues down the line.
Scalability:
How to produce vector at large scale to meet global demand
Monoclonal Process
Traditional polyclonal manufacturing methods “start from scratch” each time a batch is made, making scale up a risky and unpredictable activity, often resulting in low titers, low yields, and batch failures. These factors, combined with an insecure and expensive vector production supply chain, make producing vector at a global scale difficult.
iVexSol’s Intelligent Manufacturing is unlike traditional polyclonal systems because we generate a monoclonal master cell bank where every cell is an optimized vector-producing clone, eliminating the need to develop new processes with scale up. When vector is needed, a vial is thawed from the MCB, cells are expanded to whatever scale is necessary, and vector is harvested and processed to generate “ready to use” material capable of supporting a program of any scale.
Cost of Goods:
How can iVexSol scale production without significantly increasing CMC and analytical testing?
Ultra-Scale Batches
Transient process instability/variability typically worsens as production volumes increase. This increases CMC and analytical demands and the amount of vector from each batch to enable these tests, which in turn, necessitates the production of more batches and so on.
iVexSol’s Intelligent Manufacturing scales easily from small (150 doses) to ultra-scale batches (1000+ doses) precluding the need for multiple 200L batches and the costly CMC activities associated with each production run. In addition, ultra-scale batches also reduce clinical variability, averting unplanned trial extensions/expansions to achieve clinical significance.
harvested and processed to generate “ready to use” material capable of supporting a program of any scale.
As you prepare a drug for launch it is critical for your raw material supply chain to be secure. Establishing a secure vector supply chain is one of the most challenging activities for cell and gene therapy companies due to the unpredictable and poorly scalable nature of traditional manufacturing.
iVexSol’s Intelligent Manufacturing avoids these challenges by generating a virtually inexhaustible master cell bank of vector-producing cells. When additional vector is needed, a vial of vector-producing cells is thawed from the MCB, expanded, the vector can then be harvested and ready for release in weeks, not months or years. iVexSol’s ability to produce “vector on demand” de-risks vector supply and avoids the need to stockpile or purchase a large inventory of vector to avoid supply issues down the line.
Traditional polyclonal manufacturing methods “start from scratch” each time a batch is made, making scale up a risky and unpredictable activity, often resulting in low titers, low yields, and batch failures. These factors, combined with an insecure and expensive vector production supply chain, make producing vector at a global scale difficult.
iVexSol’s Intelligent Manufacturing is unlike traditional polyclonal systems because we generate a monoclonal master cell bank where every cell is an optimized vector-producing clone, eliminating the need to develop new processes with scale up. When vector is needed, a vial is thawed from the MCB, cells are expanded to whatever scale is necessary, and vector is harvested and processed to generate “ready to use” material capable of supporting a program of any scale.
Transient process instability/variability typically worsens as production volumes increase. This increases CMC and analytical demands and the amount of vector from each batch to enable these tests, which in turn, necessitates the production of more batches and so on.
iVexSol’s Intelligent Manufacturing scales easily from small (150 doses) to ultra-scale batches (1000+ doses) precluding the need for multiple 200L batches and the costly CMC activities associated with each production run. In addition, ultra-scale batches also reduce clinical variability, averting unplanned trial extensions/expansions to achieve clinical significance.
harvested and processed to generate “ready to use” material capable of supporting a program of any scale.
Meet iVexSol’s Intelligent ManufacturingTM
How does it work?
iVexSol’s next-generation stable lentiviral vector production platform begins with the generation of a clonally-derived master cell bank of stable vector-producing cells for the production of your gene of interest.
Transduction
Serum-free, suspension host cells are transduced with uL quantities of plasmids.
Plasmid Engineering
Plasmids are linearized and re-engineered to include inducible constructs.
Vector Fitness Testing
We begin by fitness testing your current platform to ensure it is fit for purpose.
Selection
Cells are seeded, expanded, and screened in to identify highly productive clones.
Optimal Producer
Optimal producers are further screened for stability, functionality and safety.
MCB Generation
Optimal clones are expanded to create a Master Cell Bank.
Long Term Storage
MCB is cryopreserved and split 50/50 for off-site storage.
Vector Fitness Testing
We begin by fitness testing your current platform to ensure it is fit for purpose.
Plasmid Engineering
Plasmids are linearized and re-engineered to include inducible constructs.
Transduction
Serum-free, suspension host cells are transduced with uL quantities of plasmids.
Selection
Cells are seeded, expanded, and screened in to identify highly productive clones.
Optimal Producer
Optimal producers are further screened for stability, functionality and safety.
MCB Generation
Optimal clones are expanded to create a Master Cell Bank.
Long Term Storage
MCB is cryopreserved and split 50/50 for off-site storage.
Then, whether it be your initial production run or a subsequent run, each time you need more vector, we simply expand a vial from your bank, harvest and cryopreserve the precise amount of vector you require and then send it to you (or anywhere else in the world). On demand: All within weeks, not months of your order.
Vector On Demand TM
A quantum leap for cell and gene therapy…
iVexSol’s Intelligent ManufacturingTM uses technology that solves many of the challenges facing next generation cell and gene therapy developers
Analytical Demands
& Release Testing
& Interpretation
Safety Profile
Chain Risk
and Wait-Times
Please click the options to see how iVexSol solves the challenges
Generating vector from a uniform population of cells (in your bank) significantly reduces batch to batch variations, which minimizes variations in transduction, reducing both CMC and analytical testing.
Generation of ultra-scale batches precludes the need to repeatedly perform comparability studies on multiple batches of vector, preserving vector and reducing regulatory burden and complexity.
employing a single (ultra-scale) batch that virtually eliminates batch to batch variation minimizes the number of replicates needed, greatly simplifying clinical trial design and interpretation.
Generating vector from a thawed vial (from your bank) precludes the need for plasmids or transduction-improving reagents, greatly increasing the safety profile as compared to transient systems.
The ability to rapidly produce ultra-scale batches of vector from banks that are securely stored at multiple locations minimizes supply chain risk.
The ability to generating vector “on-demand” from a thawed vial (from your bank) in weeks rather than 9-12 months minimizes the need for companies to produce (and secure) large inventories of vector before they are needed.
Analytical Demands
Generating vector from a uniform population of cells (in your bank) significantly reduces batch to batch variations, which minimizes variations in transduction, reducing both CMC and analytical testing.
& Release Testing
Generation of ultra-scale batches precludes the need to repeatedly perform comparability studies on multiple batches of vector, preserving vector and reducing regulatory burden and complexity.
& Interpretation
employing a single (ultra-scale) batch that virtually eliminates batch to batch variation minimizes the number of replicates needed, greatly simplifying clinical trial design and interpretation.
Safety Profile
Generating vector from a thawed vial (from your bank) precludes the need for plasmids or transduction-improving reagents, greatly increasing the safety profile as compared to transient systems.
Chain Risk
The ability to rapidly produce ultra-scale batches of vector from banks that are securely stored at multiple locations minimizes supply chain risk.
and Wait-Times
The ability to generating vector “on-demand” from a thawed vial (from your bank) in weeks rather than 9-12 months minimizes the need for companies to produce (and secure) large inventories of vector before they are needed.
Want more information?
Or let us know where you are in your clinical development to learn more about how our solutions can help you now.
HOW CAN WE HELP?
CONTACT US TODAY.
iVexSol
17 Briden Street
Worcester, MA 01605